Wednesday, May 22, 2019
Heineken 3D prints a variety of parts to optimise beer production and worker safety.
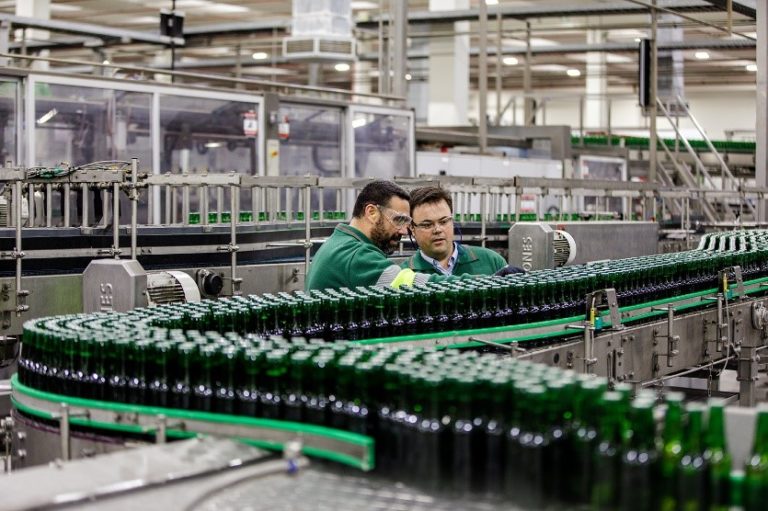
The first time we heard of a beer producer using 3D printing was to make a tap for draft beer. Today, Heineken offers an application of the technology with a variety of tools.
It was the Spanish subsidiary that integrated additive manufacturing into its production a year ago. It started using the Ultimaker 2+ printer and then several Ultimaker S5 printers.
Based in Seville, the factory produces several brands of beer belonging to the Heineken group, which accounts for around 500 million litres of beer per year.
The 3D printing technology was initially used for safety-related applications. In order to reduce production costs and save time, the beer specialist designs and prints safety devices, tools and parts on demand.
Indeed, to increase the safety of operators, intelligent 3D tools have been designed to prevent accidents. Similarly, to prevent machines from breaking down or malfunctioning, the company now relies on tools that facilitate maintenance or quality control of products or machines. Finally, a metal part that used to be used with the quality sensor on the conveyor belt often knocked over bottles, creating blockages or causing bottles to fall to the floor. By redesigning the system, operators were able to work easily with a new part.
There is no longer a need for external contractors to produce these tools. Heineken was able to reduce its costs by 80%.
Source : 3DADEPT