Tuesday, September 24, 2019
3D printing of technical ceramics has its goldsmith! Do you know 3DCERAM SINTO?
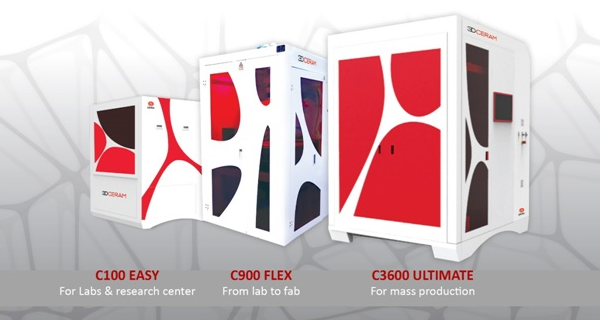
A simple consultation on the internet will give you in a few clicks just the surface of things. But not the origin of the adventure, its history and especially its future. Welcome to the field of possibilities of 3D printing of technical ceramics.
A company is above all a human story.
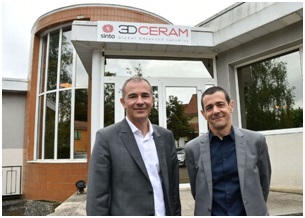
The history of 3DCERAM SINTO began in 1985 with a friendship that brought together Christophe CHAPUT and Richard GAIGNON, both ceramic engineers who had followed the same training at the École Nationale Supérieure de Céramique Industrielle (E.N.S.C.I.) in Limoges. The first began his career at MILL Cristall, a manufacturer of bioceramics, and then went on to manage the Centre de Transfert Technologique de la Céramique (CTTC). The latter completed his training with an MBA and then became General Manager and Business Director of CERIC TECHNOLOGIES, a world expert in solutions and services for the production of clay building materials.
In 2001, the CTTC decided to create a subsidiary to implement the solutions resulting from its research and entrusted its president to Christophe CHAPUT. The company, then called CeramPilot, produces components for major high-tech industrial groups.
"Beyond our friendship, we needed new challenges
In 2009, the two friends decide to launch themselves "perhaps by unconsciousness, in an improbable challenge" confides with a smile Richard GAIGNON, hence the joint purchase of the company which then becomes
3DCERAM. They opted for an ambitious strategy to differentiate themselves from the existing offer. The credo of the two developers can be summed up as follows: "anticipate so as not to be overwhelmed by the wave".
From the outset, 3DCERAM positioned itself in the field of 3D printing of technical ceramics. This technology enables the production of ceramic components in successive layers using a laser that polymerises a paste composed of photosensitive resin and ceramic. The parts are then subjected to a heat treatment (debinding and sintering) which eliminates the resin and densifies the ceramic.
It should be noted that technical ceramics, depending on their category, have a very wide range of mechanical, magnetic, thermal, chemical and electrical properties, all of which are remarkable. These properties include high mechanical strength, high dimensional stability (very low coefficient of expansion), low density, very high resistance to abrasion and corrosion, and exceptional chemical stability. These qualities, combined with incomparable insulating properties (thermal and electrical), make it possible to use ceramics for parts subject to high stresses in difficult environments.
In 2010, they manufactured their first 3D printer under the CERAMAKER brand. Over time, the range will expand to include printers and turnkey lines.
And, 2019 is a particularly prolific year!
- The C100-Easy, which has a 100*100*150 high plate, was launched in March. It was specially developed for laboratories (technical centres, universities or technical ceramic manufacturers' labs), which can easily carry out their tests, research and prototyping.
- The C900-Flex, with its 300*300*100 table top, can be used from prototyping to small series production. The C900-Flex is also "augmented" with a hybrid option to print multiple materials simultaneously.
- And finally, the brand new C3600-Ultimate, which allows mass production, thanks to its 4 lasers and its 600*600*300 high plate: It is possible to print, for example, large satellite mirrors or large series of foundry cores.
It should be noted that the hybridization of the entire range of machines (printing of various materials simultaneously) opens up very interesting prospects for certain industries and the demand for this type of machine will certainly increase.
Relying on its technological expertise, 3DCERAM SINTO is developing a complete offer to support its customers on technologically challenging projects: choice of the type of ceramics, elaboration of specifications, R&D, development of a 3D part up to its industrialization, its production on demand or in series, sale of CERAMAKER printers and associated consumables.
3DCERAM offers several types of ceramics formulated to be printed on CERAMAKER printers, and thanks to its expertise is also able to develop formulations on request.
An opening strategy that pays off!
In 2015, 3DCERAM's managers took on a new, bold and risky challenge: to market one of their printers, the C900, thus giving up their technology, equipment and processes. Far from weakening the company, this strategy of openness paid off: turnover took off (from 1 million euros to 4 million and soon to 5 million) and the workforce grew from 10 to 30 employees (particularly ceramic and mechatronics engineers and chemists).
Another even more decisive adventure!
The discovery of this "nugget" by an international group.
3DCERAM was indeed spotted two years ago by the SINTO group during a trade show in Japan. In the following months, Christophe CHAPUT and Richard GAIGNON were contacted by the Japanese group to study a partnership. At the end of 2017, this resulted in the acquisition of a stake in the capital of 3DCERAM. This affiliation to a global group provides (in addition to increased credibility with its customers and banking partners) additional means to accelerate its development and access to a global network, "and all this without changing anything in the governance of the company" underlines Richard GAIGNON!
A promising future!
A few months ago, Smartech Publishing presented its latest report on the evolution of ceramic 3D printing: by 2028, this industry should generate up to 3.6 billion dollars worldwide. According to the report, ceramic 3D printing will reach maturity in 2025 and become an established manufacturing technique in various sectors.
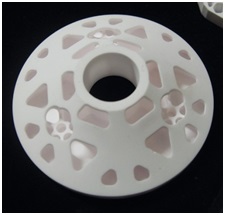
For the time being, 3DCERAM SINTO, which is building a new industrial site in Limoges, operates in the aerospace, medical, energy, defence, electrical and luxury sectors.
But this is just the beginning of the "field of possibilities"!
To find out more, visit
http://3dceram.com/fr/
Editor:
Anne de LANSALUT