Friday, March 26, 2021
Interview: Meeting with Anthony RAVIER and Additive Manufacturing
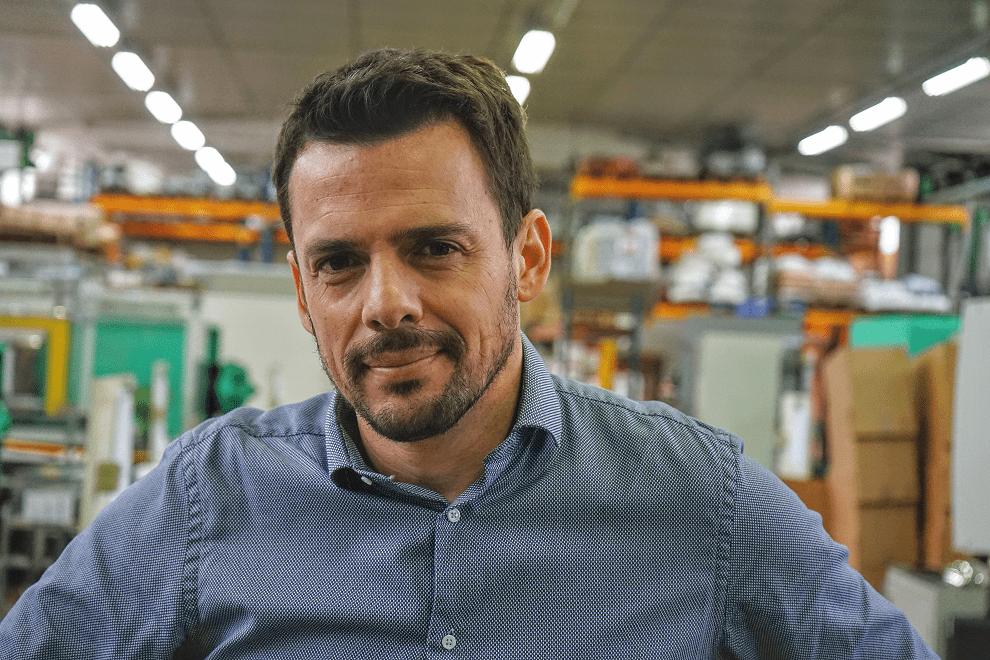
Discover the interview with Anthony Ravier, director of the company OPS Plastique. Specialising in polymer transformation, OPS has integrated additive manufacturing into the heart of its services to help its customers save tens of thousands of euros thanks to prototyping and 3D printed moulds!
Hello Mr Ravier, could you introduce yourself and summarise the main actions carried out by OPS Plastique?
Hello, I am the manager of OPS Plastique which I took over 3 years ago.
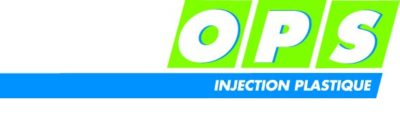
We have been transforming our customers' ideas into polymer products for 70 years. We have a real desire to offer the latest developments in plastic transformation technologies. One of them is additive manufacturing.
We offer two types of service: the manufacture of functional parts using 3D printing, which we do mainly by sintering PA12 powder, and a year ago we launched the AC3DC project, "Additive Cavities 3D Concept", which consists of producing mould cavities using additive manufacturing. We are working on this in collaboration with the company LEMANTEK. We have made several sets of cavities which have enabled us to inject parts in different materials.
How did the idea of integrating additive manufacturing into your expertise come about?
I have been interested in the world of 3D printing since 2015. Before taking over the company, I had developed PPS filaments for FDM printing on behalf of partners.
With the takeover of OPS, which specialises in the injection of medium-sized technical parts, it is in this continuity that we came to propose 3D printed polymer parts for our customers to validate the prototyping phase to meet their needs.
The fact that we saw 3D printed mould impressions at the 2019 3D PRINT show and on the POLYVIA additive manufacturing platform in LYON showed us that it was now possible to make tooling impressions in this way.
I therefore decided to launch the internal AC3DC project.
Which industries/markets use your additive manufacturing technology the most?
At the moment, we have a few examples of functional parts in 3D printing, which are used for example as consumables for production assemblies at our customers' sites, and others which are used as fuse parts in mechanical applications.
All markets or industries are very enthusiastic about us, except perhaps those that require specific regulatory aspects. I would say that as soon as the function of the part is satisfied, and the 3D printed shape or impression is feasible and compatible with the material to be used, there is only one obstacle left: the one that exists in the mind of the decision-maker.
As far as 3D printed mould imprints are concerned, our current customers are very interested in making 'good material' parts for small series, to validate functional prototypes or to mechanically test assemblies (fatigue tests for example).
Can you tell us about a success story in polymer additive manufacturing?
I don't know if it's a success story, but we recently helped one of our customers in its part design phase to test its idea with functional parts.
He wanted to make connecting parts for a product with new shapes. We worked with him iteratively to design and produce 3D printed polyamide parts to test his idea. The questions were numerous: Make 1 part? 2 parts? 3 parts? Will the parts fit correctly? Do they perform the function correctly? Are the connection gaps and the visuals correct? Many questions that we were able to answer with functional 3D printed parts.
What would have happened if the tooling, which costs several tens of thousands of euros, had been launched without this phase, only to find out 2 months later that there was a functional problem with the parts?
In the end, this is a significant gain for the customer: perhaps a little time spent in the design phase, but a gain in money and precious time in the production phase, and which avoids long and costly reworking.
Do you have any figures on the benefits obtained by your client?
For this last example, it is perhaps several thousand euros that have not been spent on reworking the mould.
As far as 3D printing tooling impressions are concerned, we have estimated that this could divide by 3 the time needed to obtain the injected part compared to that required for traditional tooling, with the added bonus of lower costs.
Contact : http://www.ops-plastique.fr/