Wednesday, November 25, 2020
New recycled plastic polymer for 3D concrete printing
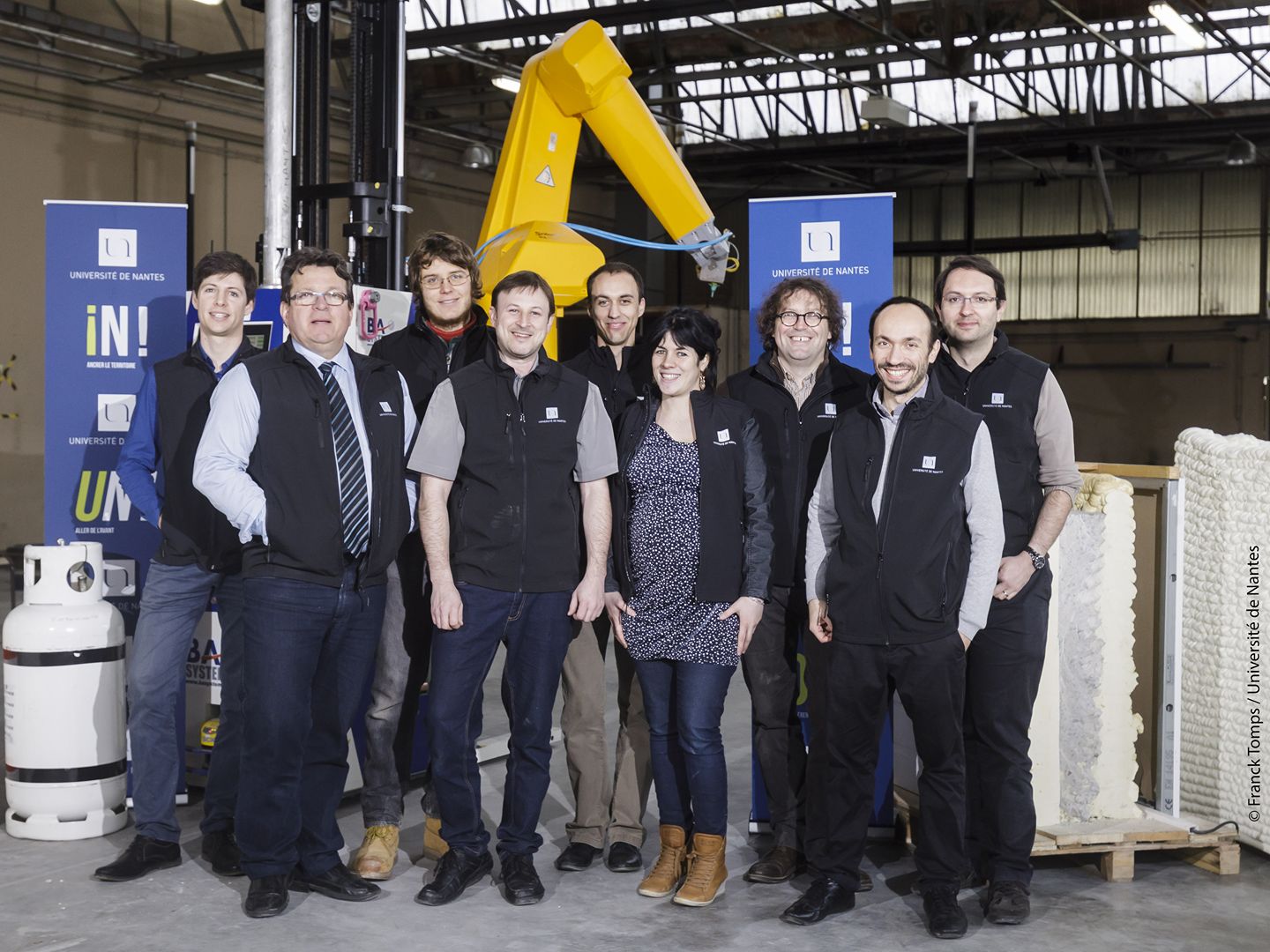
Hello Benoit Furet, can you introduce yourself and summarise the major actions carried out by the University of Nantes in additive manufacturing?
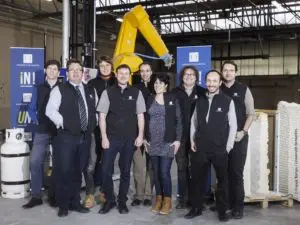
We have been working on research and teaching on additive manufacturing for almost 30 years... it's not getting any younger 🙂
Our activities first focused on the manufacturing industry and then with my colleague Sébastien GARNIER we sought to develop XXL 3D printing, before moving on to the construction field in 2015.
(Photo credit Franck Tomps for the University of Nantes)
How did the idea of developing concrete houses using multi-material 3D printing come about?
Following the natural disaster in Nepal, I had the idea of making a complete machine (robot and pump) to print emergency shelters on site... See the Innoprint3D video
From that moment, some people reacted on social networks to tell us that "the Chinese were already making "real" 3D printed houses...".
Not being a specialist in civil engineering, I researched, read, searched, travelled to China or got in touch with another colleague specialised in construction at the University of Nantes, Philippe Poullain, from the IUT of St Nazaire and the GeM lab.
After analysis, I realised that in all the experiments they were trying to print directly from mortar, and this is not easy. I said to myself that for a house, it was not only the structural part that was important, but also the thermal insulation. That's why we developed XXL multi-material 3D printing with robots to make complex walls (mechanical and thermal control).
After discussions with Nantes Métropole and the social landlord NMH, we launched the first certified 3D printed house.
As an example, in September 2017 we built the 95m² YHNOVA house printed in 54 hours directly on site with a robot. The construction was certified via an ATEX by the CSTB. This house has been inhabited for more than two years by a family of five, happy with the comfort and well-being provided by the 3D shapes adapted to the environment.
Thanks to 3D printing, no trees were cut down for this construction. It is the house that has adapted to the space. Isn't the greatest advantage of additive manufacturing that it allows us to make customised products that are perfectly adapted to the customer's needs?
At the end of 2019, after meeting with a construction company manager, Hedy Zouaoui and I created the company BATIPRINT3D. Indeed, French law allows teachers/researchers to contribute to the creation of start-ups.
BATIPRINT3D's ambition is to market 3D printing machinery for construction (machine, robot, pump, associated process, specific digital chain, etc.).
In parallel, we are developing robotic additive manufacturing solutions for the thermal renovation of existing buildings. Indeed, renovating considerably minimises the impact on the environment.
You are currently developing a project with a Canadian company integrating a new polymer from recycled plastics, can you tell us about it?
Yes, we are working with a Quebec company that produces expandable foams that mix different ingredients based on recycled PET or vegetable oil. These foams are widely used in North America to insulate conventional wood-frame, brick and other types of housing.
Expandable foams facilitate large format 3D printing but have limitations. After being 3D printed, parts can be produced up to 30 to 40 times their original volume. Thermal and mechanical effects must also be controlled.
Élodie Paquet, one of our doctoral students, has developed a multiphysics approach to the digital modelling of 3D printing of expansive materials... all combined with a complete digital chain to control the depositing trajectories with machinery whose working space is smaller than the part to be produced.
How is the recycled part integrated into this project?
In all our projects we integrate these materials based on recycled PET. Now a medium-sized house printed in 3D with the Batiprint3D solution means about 13,000 recycled plastic bottles. In the long term, during deconstruction, these materials can be crushed to form insulation panels or introduced in the form of chips into concrete slabs to insulate them. They can therefore be re-used.
Do you have any other projects in progress or coming up soon?
The next project will be a 130m² two-storey house, built with and for the company ERB-Bâtiment (49), in an eco-neighbourhood in the town of Beaucouzé (49).
The house will be built using Batiprint3d principles for multi-material 3D printing. The production of prefabricated elements will be carried out in the workshop and for the rest, directly on the building site using a robot.
For the design of the house, we used our DFC or DFAM (Design for Construction or for Additive Manufacturing) approach. The shapes will be optimised according to the needs of the future inhabitants, the construction site, the solar orientation and the existing environment. We will use virtual and augmented reality tools designed by the Nantes-based start-up PIRO-CIE, a partner of Batiprint3d.
It is important to note that 3D printing and the choice of associated materials contribute to the environmental performance of the house, which according to the new RE2020 regulation will be classified as E2C1. Indeed, the amount of material is adjusted according to the need and the 3D shape of the house will contribute to the energy performance. This is what can be called: eco-sizing.
For more information: https://www.batiprint3d.com/fr