Wednesday, November 25, 2020
A revolutionary process for the world of custom composite parts
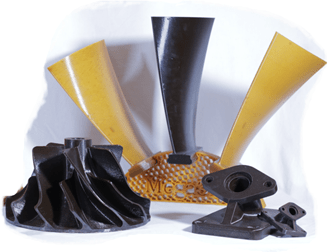
Hello Yvan Sampic, can you introduce yourself and MEGA 3D?
Hello, I am Yvan Sampic, founder and Ceo of Mega3D. I've always been passionate about new technologies and I'm fascinated by Additive Manufacturing and its ever-pushing limits.
Mega3D is an innovative company specialised in large-scale additive manufacturing with specific materials. R&D, adaptation and creativity are our daily work to develop a special machine or a process.
How did the idea of developing large format 3D printing with foundry wax come about?
The Mega3D adventure began in 2013 with the design and production of a large FDM machine (1.5 cubic meters) using conventional polymers (PLA, PETG, etc.). This machine was quickly upgraded to print wax models at the request of an art foundry. In 2016, one of the first achievements was the enlargement of the giraffe statue in the Parc de la tête d'or to obtain a 4m high bronze in 2016.
Which sectors are using this technology the most?
The art foundry is now the main user of this technology to produce single works or enlargements. Digital sculpture is also booming and the direct 3D printing of foundry wax proposed by Mega3D represents an excellent means of realising this mode of expression.
We also work for the industry in partnership with the technical centre of the foundry and lost wax industries. The possibilities linked to our technology are still unknown and deployment takes time, but I remain convinced of its potential for unit parts or small series in the field of machine maintenance, for example.
Do you have any current or future projects?
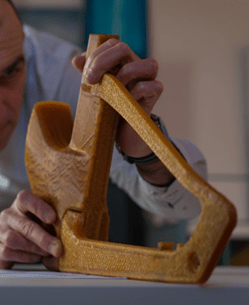
At Mega3D there is never a shortage of projects!
As I have already told you, R&D is one of our main activities. So two important projects are underway. The first one concerns the direct additive manufacturing of ceramics, this project being confidential I cannot tell you more about it. The second concerns composite materials in indirect FA. In partnership with the company Twillbee (it was at 3DPrint 2019 that I met Xavier Roussin-Bouchard), we are developing a revolutionary process for the world of custom composite parts. Our technology should allow the production of hollow composite parts without investment with a drastic reduction in manufacturing time. With the virtual elimination of tooling, we will move very quickly from digital to functional parts with the possibility of customising the geometry or structure and evolving the design. Less financial exposure in the event of market changes, the possibility of producing to order and being an early adopter of the latest component standards will bring agility.
www.Mega3D.fr
contact@mega3D.fr
contact@mega3D.fr